Managing a Manufacturing Business is a tough Job
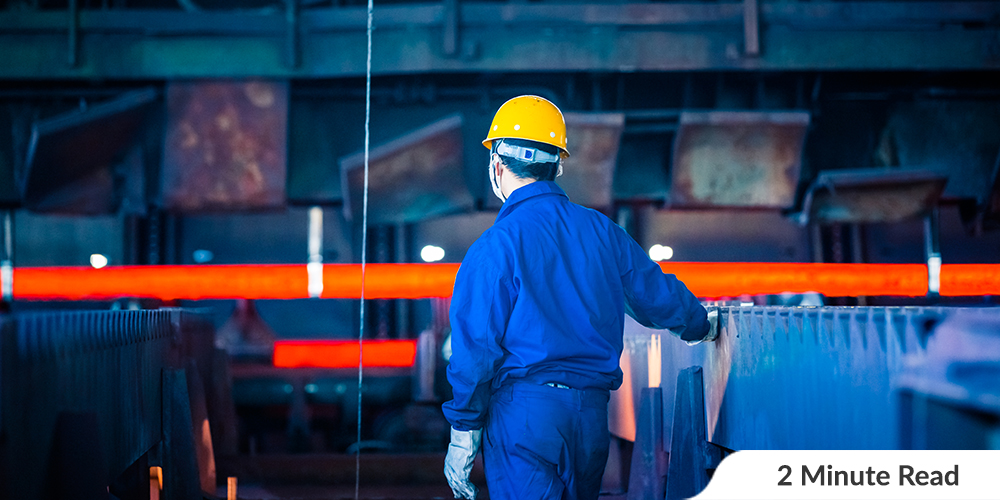
A manufacturing business deals with some tight deadlines to produce high-quality end-products. It is vital to keep your employees motivated in this highly competitive working environment. Check out these tips listed in the article to encourage your employees.
MANAGING A MANUFACTURING BUSINESS IS A TOUGH JOB
No matter how big or small your manufacturing business is, efficiency and productivity relative to capital invested is the key to gain a competitive edge over other manufacturers. However, the manufacturing industry faces a myriad of challenges that some other industries do not really encounter.
Due to these challenges, business leaders in the manufacturing industry need to have a strategic business plan to detect and mitigate any problems that may arise. The practice of management is undergoing a paradigm shift and instead of focusing on just linear improvements, one should focus on radical enhancements too.
Profit matters more than quantity
Forcing workers to meet unrealistic manufacturing output targets is a wrong approach that many manufacturing industries follow. Instead, have your workers understand how they can contribute to the profits of the company – that they’re not just a number. Introduce a rewards program for them that get better as the team adds more to the bottom line.
Focus on process and results will follow
No doubt one works day and night with a goal of results, but if you ignore the ‘process’ that leads to this event, you end up losing the focus and dedication of your employees. When you focus on the process as a whole rather than smaller parts it helps aids your employees in wanting to reach that goal. Recognize workers who go above and beyond in their efforts as a way to motivate your team.
Recognizing an employee for his good work is not as hard as you may think in today’s digital world. Recognizing and rewarding them is easy through the Ezzely employee engagement app with points or encouraging words.
Follow the ‘Kaizen’ approach
Kaizen is a Sino-Japanese word that means “change for better”. It is most commonly referred to by lean manufacturers as the practice of “sporadic improvement.” Kaizen is defined as a long-term approach to work systematically to achieve small, incremental changes in processes in order to improve efficiency and quality.
Motivate and encourage your workers to continually improve processes on a daily basis. Even a small percentage of improvement will matter a lot in the long run. Workers are more close to production than any other designated employee of the company, so boost them to come up with more and more ideas to improve production.
Reward and recognize employees the one who comes up with the best idea. Innovative companies are seeking the help of new mobile apps like Ezzely that provide a robust platform for peer recognition across the company. You never know, a small change today can result in higher production tomorrow.
Toyota’s approach to manufacturing is a prime example of Kaizen in action.
Harness a culture of collaboration
The manufacturing plant is most productive when each and every employee communicates openly towards a single goal. Replace the traditional suggestion box with mobile apps like Ezzely that can help to harness a culture of collaboration. Incorporating such kinds of tools involve your team in solution-oriented conversations that can pave way for higher worker satisfaction and productivity.